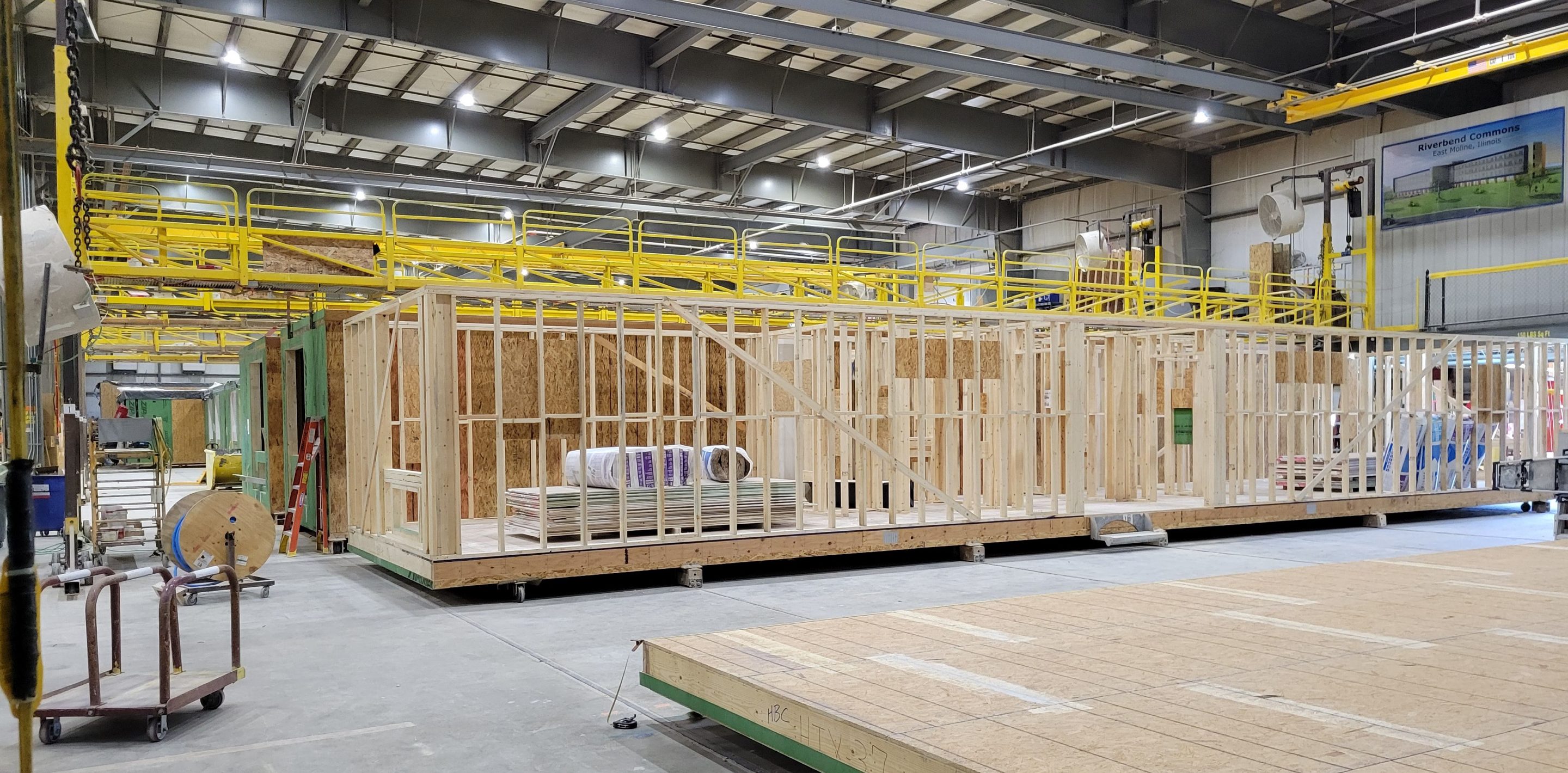
As the number of ‘Baby Boomer’ retirements increase and life expectancy continues to grow, the demand for senior living continues to rise. The Joint Center for Housing Studies by Harvard University notes “The US population 65 and over soared by 34 percent in the last decade… In the coming decade, the fastest growth will occur among those over 80, when people are more likely to need accessible housing.”* In the wake of recent market conditions, such as inflation and soaring construction costs, senior living development has slowed and reaching the forecasted demand is becoming increasingly difficult. Given this climate, alternate methods of construction can provide opportunities to make construction more affordable while, simultaneously, bringing new developments to the market at a pace that can better meet the growing demand.
To help meet the increased demand for senior living and address the realities of our current financial market, modular construction provides a route to address these challenges, which are particularly prevalent in the middle market. This unique method of construction blends efficiency, affordability, and quality, assembled within a controlled environment and shipped to the site for final installation. Capitalizing on off-site fabrication techniques, modular construction accelerates the building process while significantly reducing both time to market, unforeseen expenses and unpredictable weather delays.
This construction methodology provides efficiency in design and functionality to cater to the unique requirements of various care levels and project types such as:
- Independent Living (IL)
- Assisted Living (AL)
- Short or Long Term Skilled Nursing (SN)
- Memory Care (MC)
- Multi-family Residential
- Student Housing
- Hotels
In this article, we explore the applicability of modular construction to address some challenges in the middle market for senior living and multifamily housing and some of the benefits of this method of construction.
What is modular construction?
Modular construction is a methodology which assembles sections of a building, or modules, in a factory-controlled setting to be shipped and assembled in the field. Each module is structurally independent including floor, wall and ceiling assemblies engineered to ship to construction sites and attached to a substructure, or additional modules. Plumbing, mechanical and electrical infrastructure run through the module floor and ceiling assemblies and connect to surrounding infrastructure when assembled on site. Corridor sections of the module are typically left unfinished allowing access for final connections. Typically, individual modules measure from 14-17’ wide and 50-70’ long, dictated by the constraints of the shipping process. Each module consists of a bedroom or living area of two cross corridor apartments, and the circulation corridor between them. The living spaces within the module are fully finished, accessorized, and furnished. In this method of construction, the general contractor is responsible for site utilities, infrastructure connections, foundations/slabs, the exterior façade, roofing, and the finishing of the corridor spaces. Given the uniqueness of modular construction, having a partner experienced and familiar with process is essential to its success.
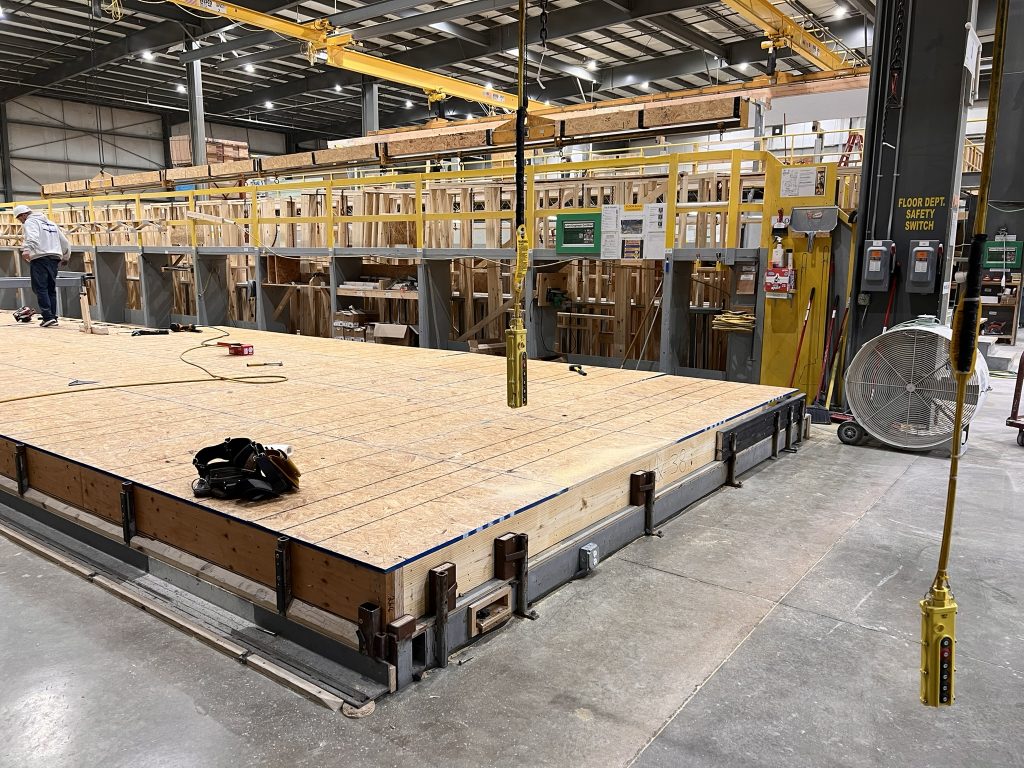
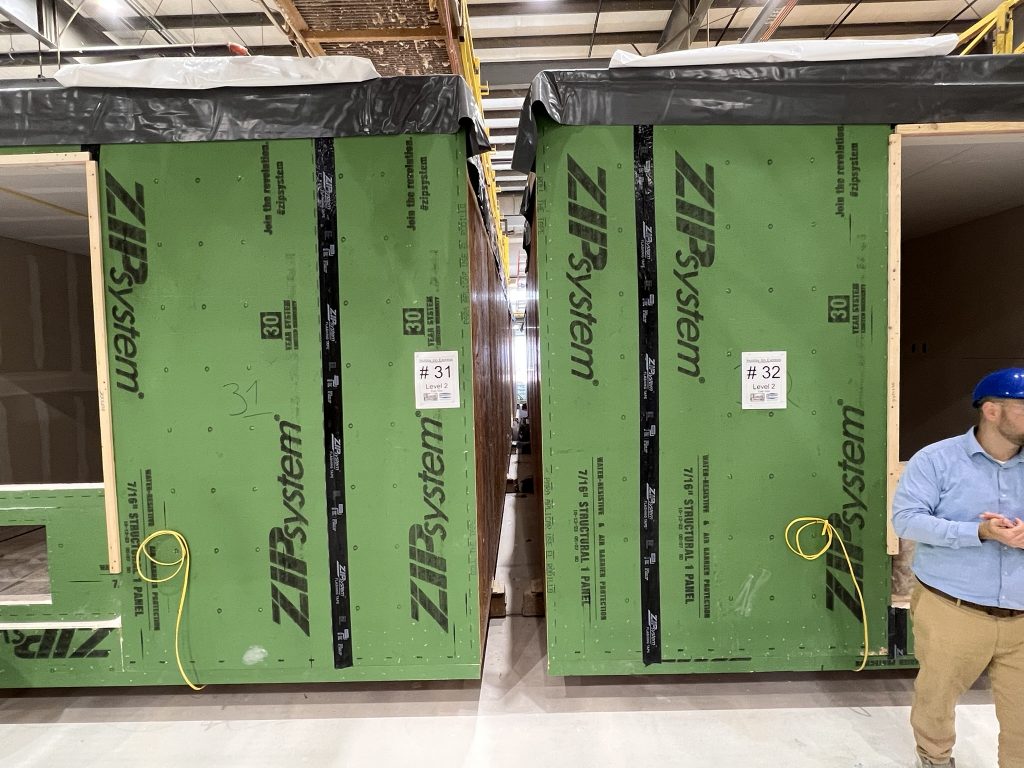
Modular construction can be accomplished in wood or cold form metal framing options, depending on the manufacture’s capabilities. Which option depends on building code requirements and what the local authority having jurisdiction (AHJ) will allow, as well as any state health departments. It is common for a modular manufacturer to have their assembly line set only for one construction type, so early identification of which modular company to work with is a critical first step.
This construction methodology is newer to the market, so coordination with local, state, and regulatory agencies is a critical first step to get buy in from the necessary parties. Early understanding and approval by the authority having jurisdiction on how factory inspections take place through a third-party inspector must be agreed upon in order to make this construction methodology achievable.
Why can modular construction be more efficient?
As modules manufactured concurrently with the site preparation, buildings are completed in significantly less time compared to traditional construction methods. This repetition of a specific size module lends itself to smaller middle market apartments and quick site erection. A hybrid approach allows for the integration of modular and conventional building techniques to optimize efficiency. Modular construction does not need to be a stand alone component in the process, but more as a part of the overall sequencing and design solution.
Architect: Early coordination of the modular process needs to be adopted by the architect and engineering teams to maximize the modular design potential. This process should be intentionally coordinated at the beginning of the project, rather than as a value engineering option after the design is complete. Understanding the modular manufacturer’s standards is important for architectural detailing, working within modular dimensional standards, and navigating material selections, transportation, and procurement challenges. Once plans are complete and approved, finish materials selected and site coordination has been scheduled, the assembly of the modular units will commence utilizing an assembly line approach until fabrication of all units are complete. This assembly line moves along from rough framing to utility installation to final finishes. Near completion the architect and engineers complete punch list reviews in conjunction with code official inspections signing off on all code compliance. Then the modules are packaged for delivery and assembly onsite. The architect and a representative of the modular manufacturer will observe installation on site for QA/QC, similar to typical construction.
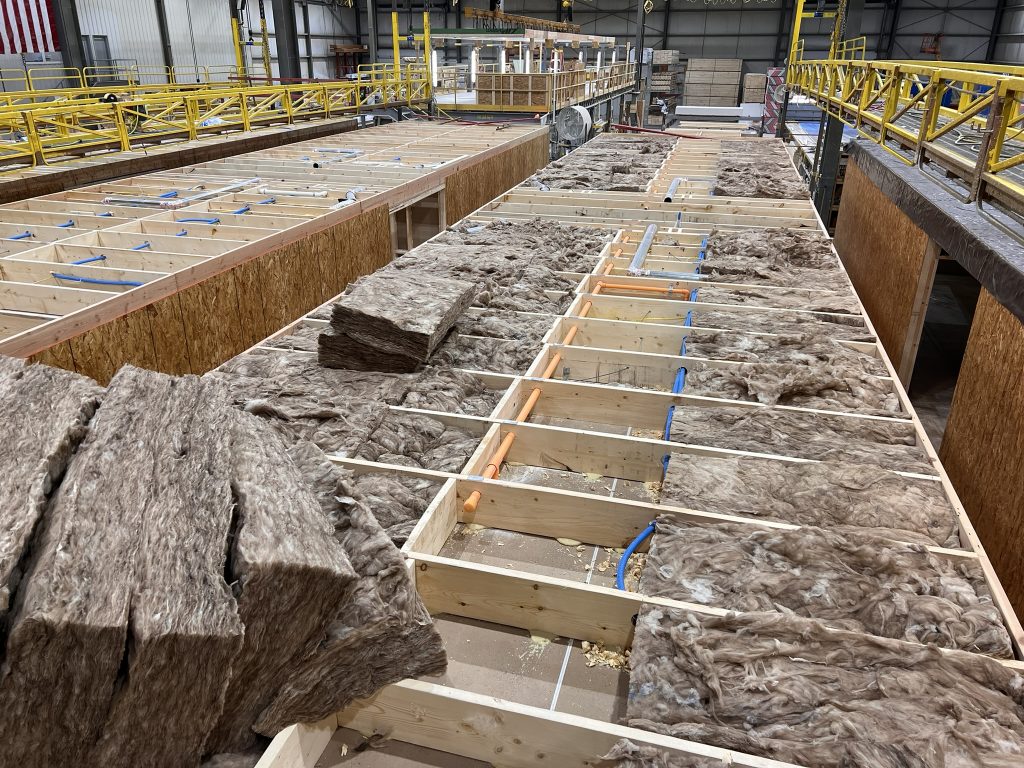
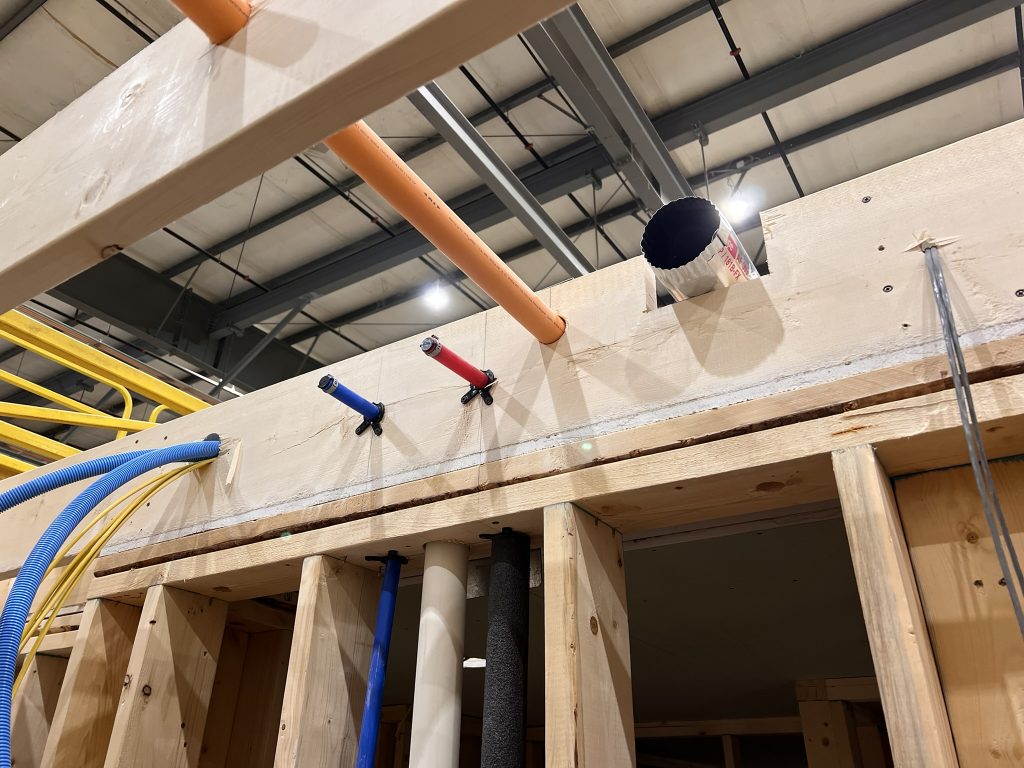
General Contractors (GCs): Engaging GCs familiar with modular construction allows better coordination between off-site manufacturing and on-site assembly earlier in the process. Efficiency is achieved as modules are constructed in the factory while on-site construction such as: foundations, floor slabs, site infrastructure, and grading activities continue simultaneously in the field. Ensuring that the GC understands on site vs. off site material procurement, modular delivery scheduling and installation sequencing is crucial to take advantage of this efficiency.
Engineering: MEP/FP and structural systems are integrated into the parameters of the assembly. Each module contains all the piping and connections for infrastructure, run through the floor-ceiling assemblies, and are ready for final connections in the field. With each structurally independent modular unit having integrated MEP systems, field installation becomes more akin to an assembly of parts pre-designed by the engineers to limit field complications with site built portions of a project.
How is modular more affordable than traditional construction?
Controlled factory assembly reduces labor expenses, minimizes material waste, and can shorter construction durations all to the benefit of senior living operator and owner’s overall project costs. Due to the construction methodology and a majority of the building being constructed in a controlled environment by one sub contractor, a reduced level of risk creates the potential to decrease construction contingency.
Reduced construction schedule duration becomes the biggest contributor to lower costs. Modular fabricators suggest a potential savings of up to 30-40%, depending on the design complexity and on-site coordination. Since modular manufacturing limits time on site the contractor’s general conditions can be reduced, and earlier occupancy may reduce ownership’s financing costs.
Does modular construction negatively impact the overall design or quality of the project?
No, while some previously discussed dimensional requirements must be adhered to, incorporating necessary standards early on allows the architect to provide creative designs with many different solutions. Modular fabricators have pre-existing relationships with high volume product partners ensuring higher end products and finishes can be incorporated into a design without resorting to a lesser product, or deal with procurement struggles.
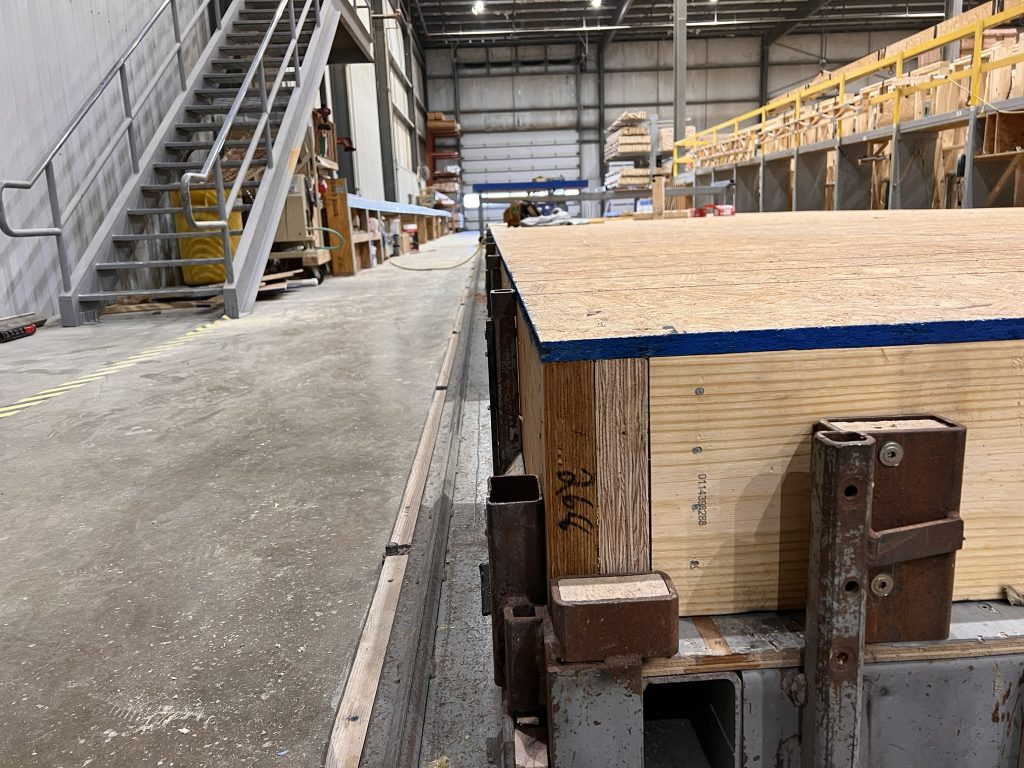
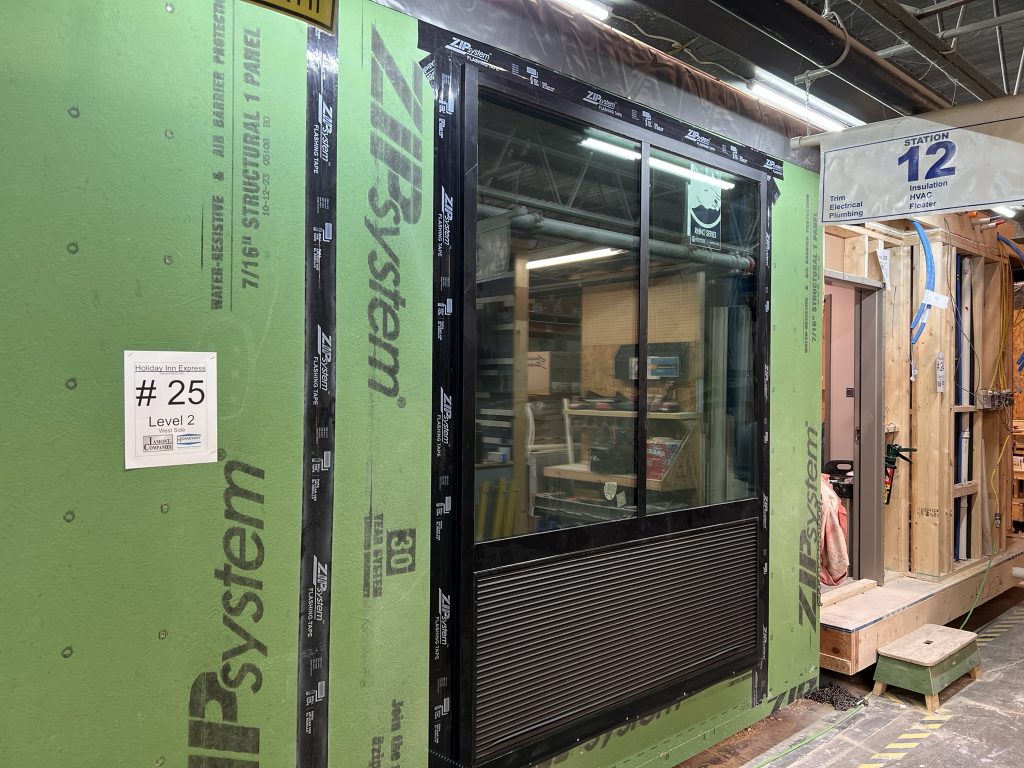
The construction quality of the building can exceed traditional construction. A factory-controlled environment ensures consistent precision by utilizing jigs and rigging to provide consistency in the process. The factory setting also limits the impact of weather in the construction process, which traditionally occurs prior to weatherproofing the building. Increased oversight of the MEP systems improves general oversight from a traditional job site.
What are the limitations to modular construction?
A discussion of the efficiency, cost effectiveness, and quality of modular construction cannot be complete without addressing some of the possible limitations to the system and why it may be better suited for the middle market. The dimensional restrictions limit the size of residential unit modules, and can affect the degree of openness within an apartment design based on bearing wall conditions and connections. This inherit efficiency in modular construction standardizes floor plans. While working within dimensionally limited modules works better for moderately sized middle market apartments, higher-end apartments may not be able to achieve larger and more open layouts due to these restrictions.
Due to the efficient and repetitive nature of modular construction, it is extremely difficult to accommodate design changes once construction begins. Resident / depositor personalizations are reduced since the approval process and decision timeline disrupts the assembly line approach to construction. This does not mean there are no options for a resident, just that the options have to be preselected across unit types by the design team and owner/developer prior to start of construction, rather than waiting on selections from the resident. Once the process begins opportunities for owner changes are eliminated, so it is crucial that all reviews and approvals are thorough and completed prior to construction.
Conclusion
Caroline Pearson, with NORC (National Opinion Research Center) at the University of Chicago, discusses the struggles of middle-income seniors in her research essay ‘The Forgotten Middle’, noting: “The private seniors housing industry has generally focused on higher-income people instead. We project that by 2029 there will be 14.4 million middle-income seniors…. we project that 54 percent of seniors will not have sufficient financial resources to pay for it.”**
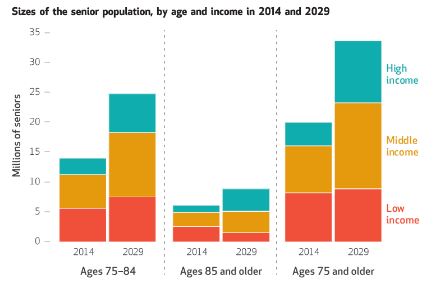
Readjusting the senior housing industry’s focus on addressing the needs of the middle market requires designers, owners, operators, developers, and contractors to assess their project design, construction, and delivery methods. Modular building construction stands out as a realistic and achievable avenue to reduce construction costs and schedules, without sacrificing quality. Through innovation in architecture and buy-in by the development team, modular design can be part of the solution to reach this underserved market and address this critical need.
Citations:
- Slat, B. (2023, Nov. 23). As the Older Adult Population Soars, US is Unprepared to Provide Housing and Care for Millions of People. JCHS – Harvard Univeristy. https://www.jchs.harvard.edu/press-releases/older-adult-population-soars-us-unprepared-provide-housing-and-care-millions-people
- Pearson, Caroline F. (2019, May) The Forgotten Middle: Many Middle-Income Seniors Will Have Insufficient Resources For Housing And Health Care. Health Affairs. https://www.healthaffairs.org/doi/pdf/10.1377/hlthaff.2018.05233